Exploring the High Standards of a China CNC Turning Part Factory
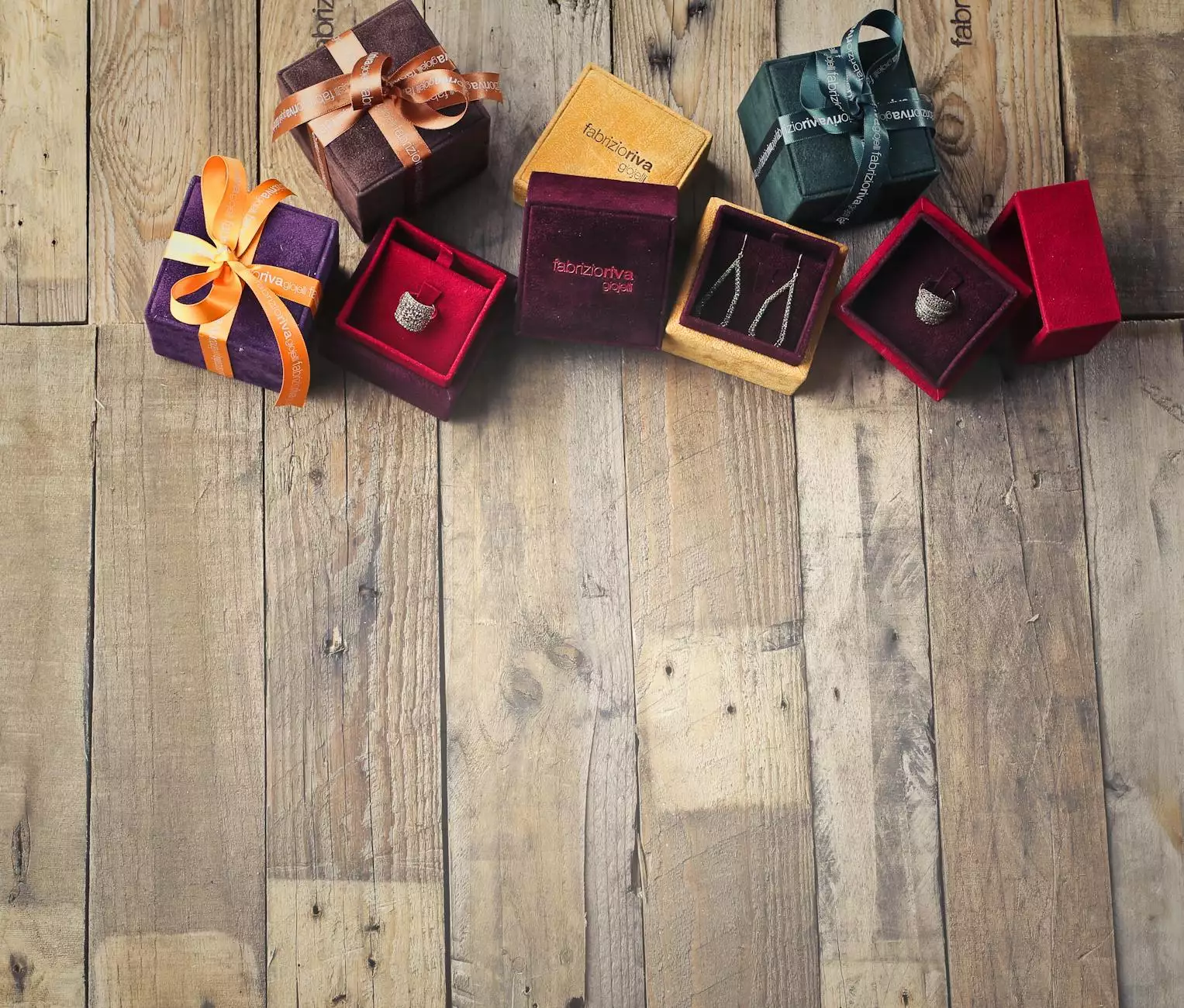
In today’s competitive manufacturing landscape, the demand for precision-engineered components is at an all-time high. Among the leading technologies meeting this demand is CNC (Computer Numerical Control) machining, which includes processes like CNC turning. This article will delve into the benefits and intricacies of working with a China CNC turning part factory, emphasizing excellence in metal fabrication.
The Essence of CNC Turning Technology
CNC turning is a precise manufacturing technique that utilizes computer-controlled machinery to produce cylindrical parts. The turning process involves the rotation of the workpiece while a cutting tool is fed into the material to create the desired shape. This method is renowned for its ability to produce complex geometries with high accuracy and repeatability.
Key Advantages of CNC Turning
- High Precision: CNC turning machines operate with exceptional accuracy, often achieving tolerances as tight as ±0.001 inches.
- Consistency: Automated processes ensure uniformity across large production runs, reducing variability and scrap rates.
- Flexibility: Different materials can be used, including metals, plastics, and composites, allowing for versatile applications.
- Efficiency: CNC machines can operate continuously, reducing lead times and operational costs.
- Complex Design Capability: Advanced software allows for intricate designs that would be impossible to achieve manually.
Choosing a Reliable China CNC Turning Part Factory
When selecting a China CNC turning part factory, several factors must be considered to ensure that your production needs are met effectively. Here are key aspects to keep in mind:
1. Expertise and Experience
Look for a factory with a proven track record in CNC machining. Experienced manufacturers understand the nuances of different materials and can provide insights into the machining process that can save both time and costs.
2. Quality Assurance Processes
Quality should be at the forefront. A reputable factory will have stringent quality assurance measures in place, including:
- Regular Equipment Calibration: Ensures machines operate within specified tolerances.
- Material Inspections: Verifying the quality and specifications of raw materials before production.
- Final Part Testing: Conducting rigorous tests on finished products to ensure adherence to client specifications.
3. Advanced Equipment and Technology
The latest CNC machines and software can significantly enhance production capabilities. Factories that invest in modern technology can often deliver superior quality and faster turnaround times.
4. Customization Capabilities
Each client may have specific needs for their components. A capable factory should be able to offer custom solutions, from design modifications to unique material choices, ensuring your unique specifications are met.
The Metal Fabrication Process in a China CNC Turning Part Factory
The metal fabrication process encompasses several stages, each crucial for producing high-quality CNC turned components:
1. Design and Prototyping
Everything begins with a design. Engineers create detailed 3D models using CAD (Computer-Aided Design) software. Once the design is finalized, a prototype may be developed to validate the design before full-scale production.
2. Material Selection
Choosing the right material is critical. Factors such as strength, weight, corrosion resistance, and thermal properties play a significant role in material selection. Commonly used materials in CNC turning include:
- Aluminum: Known for its light weight and resistance to corrosion.
- Stainless Steel: Offers high strength and resistance to rust and wear.
- Brass: Ideal for applications requiring excellent machinability.
3. Machining
The actual machining involves programming the CNC machine with precise parameters dictated by the design file. The machine then executes the turning operations with minimal human intervention, which enhances precision.
4. Finishing
After the turning operations, parts may require additional finishing processes like sanding, polishing, or anodizing to enhance their appearance and functionality.
5. Quality Control
The final stage in the fabrication process is quality control. Finished parts are thoroughly inspected using sophisticated measurement tools to ensure they meet the required specifications.
Applications of CNC Turning Parts
CNC turning parts are crucial across various industries. Some prominent applications include:
- Aerospace: Precision components that can withstand high stress and extreme temperatures.
- Automotive: Parts such as gears, shafts, and fittings that require high durability.
- Medical Devices: Components that must adhere to strict health regulations and be highly reliable.
- Consumer Electronics: Small intricate parts necessary for the function of electronic devices.
Cost Considerations in CNC Turning Manufacturing
Understanding the cost factors related to CNC turning manufacturing is essential for businesses looking to utilize these services effectively. The primary components affecting costs include:
1. Material Costs
The choice of material directly impacts cost. Higher-grade materials may provide superior performance but at an increased expense.
2. Complexity of Design
More complex designs that require intricate machining will typically incur higher labor and machining costs.
3. Quantity
Production volume will influence the cost per part. Bulk orders often benefit from economies of scale, reducing individual part prices.
4. Lead Times
Rushed orders may incur additional fees. Planning ahead can help mitigate these costs and ensure timely delivery without added expenses.
Sustainability and Environmental Considerations
Modern manufacturers are increasingly aware of the environmental impact of their operations. A top-tier China CNC turning part factory will implement sustainable practices such as:
- Efficient Waste Management: Reducing scrap and recycling materials whenever possible.
- Energy-Efficient Machinery: Utilizing machines that minimize energy consumption during operations.
- Eco-Friendly Materials: Sourcing materials that are recyclable or have lower environmental impact.
The Future of CNC Turning Technology
The realm of CNC machining continues to evolve, with advancements in technology paving the way for greater efficiency and capabilities. Key trends shaping the future include:
1. Increased Automation
Automation will enhance production speed and reduce human error, further pushing the boundaries of what CNC turning can achieve.
2. Integration with IoT
The Internet of Things (IoT) will allow CNC machines to communicate data in real-time, facilitating predictive maintenance and improved production planning.
3. Advanced Materials
Research into new materials will enable the creation of components with enhanced properties, further expanding the application range of CNC turning.
Conclusion
Partnering with a reputable China CNC turning part factory can dramatically enhance your manufacturing capabilities, providing high-quality, precision-engineered components tailored to your specifications. The combination of advanced technology, skilled workmanship, and stringent quality control makes CNC turning an invaluable process in the metal fabrication industry.
As the manufacturing landscape continues to grow, embracing the benefits of CNC machining positions businesses to leverage efficiency, reduce costs, and sustain competitiveness in their respective markets. If you are looking to elevate your manufacturing processes, consider the superior offerings of a top-tier CNC turning factory in China.